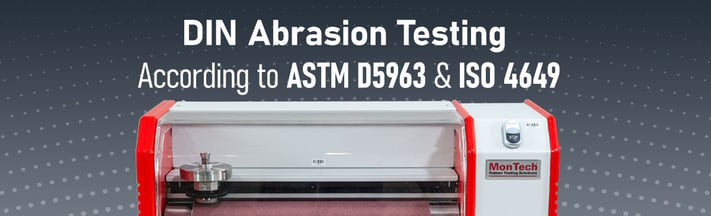
DIN Abrasion Testing, guided by ISO 4649 and ASTM D5963, is a fundamental method for assessing the wear resistance of rubber materials. This test is crucial in determining how rubber products will perform under conditions of continuous friction and abrasion. In this article, we will explore the apparatus used, the procedure of the test, and the importance of DIN Abrasion Testing in ensuring the quality and durability of rubber materials.
Apparatus for DIN Abrasion Testing
The DIN Abrasion Tester is designed to simulate real-world abrasive conditions that rubber materials face in various applications. The key components of the apparatus include:
|
 |
- Rotating Cylindrical Drum
- The drum is covered with a specified abrasive paper. The drum rotates at a controlled speed, providing a consistent abrasive surface for testing.
- Sample Holder
- The rubber sample is mounted on a holder, which ensures it is pressed against the rotating drum at a consistent force and angle throughout the test. The sample holder has two primary modes of operation, stationary and rotational.
- Abrasion Paper
- The abrasive paper used on the drum is standardized to ensure uniform testing conditions. This ensures results are comparable when also utilized with a standard test elastomer.
- Force Application Mechanism
- This mechanism applies a specified force to the sample, ensuring consistent pressure against the abrasive drum.
Procedure for DIN Abrasion Testing
The DIN Abrasion Test is performed following a structured procedure to ensure accurate and repeatable results:
- Sample Preparation
- The rubber sample is prepared to specific dimensions, typically in the form of a rectangular strip. The sample’s initial volume or weight is measured accurately.
- Mounting the Sample
- The prepared sample is mounted on the sample holder. The holder ensures that the sample is positioned correctly against the rotating drum.
- Testing Conditions
- The drum, covered with the abrasive paper, rotates at a specified speed of 40rpm The sample is pressed against the drum with a defined force. Typically 10N
- Abrasion Process
- The sample is abraded for a predetermined number of cycles No, not number of cycles but distance or until a specified volume of material has been worn away. No The drum’s rotation and the force applied ensure consistent abrasion.
- Measurement and Calculation
- After the test, the sample is removed, and its weight is measured. It is advised that density be a known value for the material so that abrasion may be calculated.
Importance of DIN Abrasion Testing
DIN Abrasion Testing is crucial for several reasons:
- Predicting Product Lifespan
- By measuring the wear resistance of rubber materials, manufacturers can predict the lifespan of rubber products. This information is vital for designing products that meet longevity expectations. Especially for tire and conveyor belts.
- Ensuring Quality and Consistency
- Consistent abrasion testing ensures that rubber materials meet industry standards and customer expectations. This quality control step is essential for maintaining the integrity of the supply chain.
- Comparing Materials
- DIN Abrasion Testing allows for the comparison of different rubber compounds. Manufacturers can select the best material for specific applications, optimizing performance and cost-effectiveness.
- Enhancing Safety and Reliability
- In critical applications, such as automotive tires and industrial belts, ensuring the abrasion resistance of rubber components is vital for safety and operational reliability.
- Meeting Industry Standards
- Compliance with ISO 4649 and other industry standards ensures that products meet the rigorous demands of their intended applications. This compliance is often a requirement for market acceptance and regulatory approval.
MonTech ABR 3000:
The MonTech ABR 3000 is quickly becoming the standard for in-house DIN abrasion analysis. Constructed with the highest quality materials and backed by a global team of material experts and technicians, the instrument can be placed in R&D or Quality Control settings with ease. All ABR 3000 units come optional with additional abrasion sheets, reference elastomers, sample drilling knives, automated cleaning units, and more.
Specialized versions of the DIN rotary drum also exist for different applicational requirements, including heated drums for checking abrasiveness at elevated temperatures and wet abrasion for checks under wet conditions.
Furthermore there are specialized versions of the DIN Rotary drum abrader available catering to different application requirements such as heated drums for checking abrasiveness at elevated temperatures as well as wet abrasion to check abrasiveness under wet conditions.
Conclusion
DIN Abrasion Testing according to ASTM D5963 or ISO 4649 is an essential method for evaluating the wear resistance of rubber materials. By using a standardized abrasion tester and procedure, this test provides valuable insights into the durability and performance of rubber products. Ensuring high-quality, long-lasting materials through rigorous abrasion testing is crucial for a wide range of industries, from automotive to consumer goods.
To learn more about the ABR 3000 Abrasion Tester Click Here!