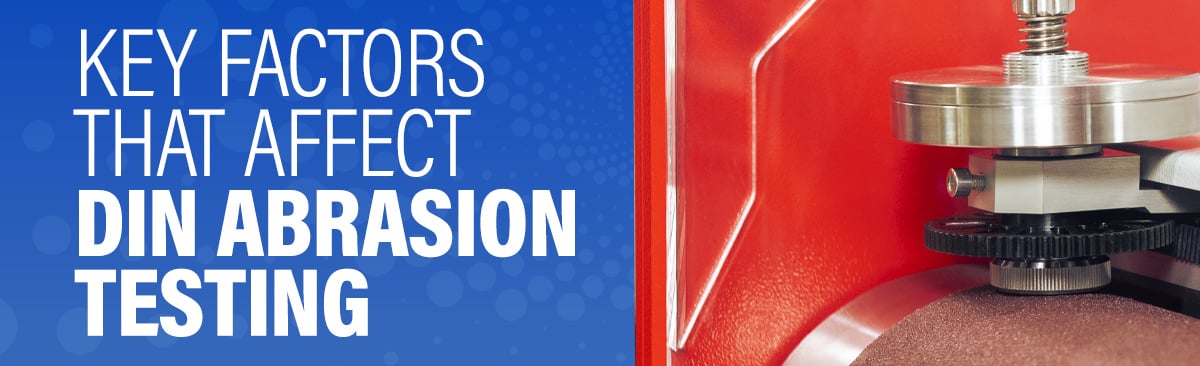
A DIN Abrasion Tester is a specialized instrument used to evaluate the abrasion resistance of rubber materials. This test is crucial in determining how well a rubber formulation can withstand wear and tear over time, particularly in applications where the material is exposed to constant friction or abrasive environments, such as tires, conveyor belts, or footwear soles.
How does a DIN Abrasion Tester work?
Following ASTM D5963, the DIN Abrasion Tester works by subjecting a rubber sample to controlled abrasive action under specified conditions. The small rubber sample is mounted on a rotating drum covered with abrasive paper. A predefined load of 10kN is applied to the sample, and it is abraded over a set distance or time on the abrasive sheet. The amount of material lost due to abrasion is then measured, typically in cubic millimeters, which gives a quantifiable value of the material's abrasion resistance.
Factors Affecting DIN Abrasion Resistance
Several properties of a rubber formulation can directly impact its DIN abrasion resistance. Understanding these factors is crucial for developing materials tailored for high-performance applications.
- Hardness: Generally, harder rubber compounds tend to have better abrasion resistance. However, this is not always a straightforward correlation, as excessively hard materials may become brittle and more prone to cracking, which can reduce abrasion resistance.
- Filler Content: The type and amount of filler used in a rubber formulation significantly influence its abrasion resistance. For instance, carbon black is a common filler that enhances abrasion resistance by reinforcing the rubber matrix. However, the balance between filler content and other properties like elasticity must be carefully managed.
- Polymer Type: The base polymer of the rubber compound plays a critical role in determining abrasion resistance. Polymers with higher molecular weight and stronger intermolecular forces, such as natural rubber (NR) or butadiene rubber (BR), typically offer superior abrasion resistance compared to others like styrene-butadiene rubber (SBR).
- Crosslink Density: The degree of crosslinking within the rubber matrix, often controlled by the amount of vulcanizing agent, affects the material's wear characteristics. Higher crosslink density generally improves abrasion resistance by creating a more robust network that resists wear. However, over-vulcanization can lead to brittleness.
- Elasticity and Resilience: Rubber formulations with higher elasticity and resilience can absorb energy during abrasive contact, reducing wear. This is particularly important in dynamic applications where the rubber is subject to repeated deformations.
- Oil and Plasticizer Content: The presence of oils and plasticizers can affect the softness and flexibility of the rubber, which in turn impacts its abrasion resistance. While these additives can improve processing and flexibility, excessive amounts can reduce wear resistance by softening the rubber too much.
- Surface Properties: The surface finish and texture of the rubber can also play a role in its abrasion resistance. Smoother surfaces typically exhibit better abrasion resistance due to reduced friction and less opportunity for abrasive particles to catch and wear down the material.
Abrasion Matters..
A DIN Abrasion Tester provides a standardized method to assess the wear resistance of rubber materials, offering valuable insights into how a formulation will perform in abrasive environments. By understanding and optimizing the factors that influence abrasion resistance—such as hardness, filler content, polymer type, crosslink density, and elasticity—manufacturers can develop rubber products that deliver enhanced durability and performance in demanding applications.
MonTech’s DIN Abrasion Tester is perfect for determining the abrasion resistance of rubber materials. With plenty of options to choose from, including hot abrasion, wet abrasion, different load forces, or others, the unit is customizable to match any application. For more information, take a closer look at the DIN Abrasion Tester here.